
MANUFACTURERS AND SUPPLIERS OF QUALITY MARINE EQUIPMENT
|
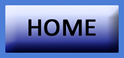 |
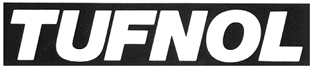 |
Appointed Australian Importer
and Distributor |
|
|
The various grade of Tufnol are manufactured at their Birmingham, England factory and were one of the first non-metallic bearing materials to hit the market in the 1920's. Originally used for switchgear, Tufnol now manufacture a wide range of materials for use in the marine, aerospace, railway, construction and electrical industries. |
|
|
Fabric Laminates and Bearing Materials |
|
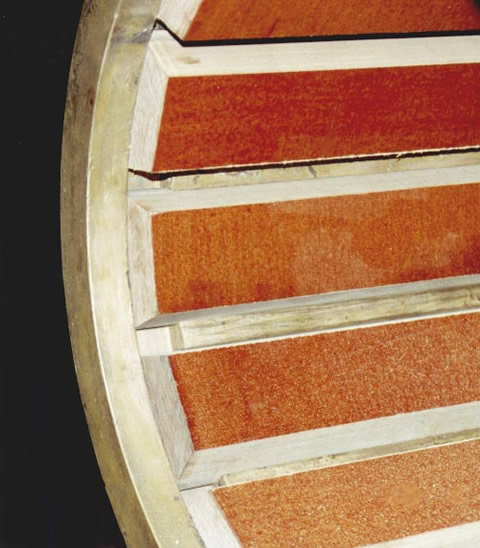 |
Bear Brand |
Specifically designed for water lubricated marine propeller shaft and rudder bearings, can also be used in oil lubricated sterntubes. |
Data Sheet |
Whale Brand |
General purpose medium weave material suitable for gears, wear resistant components and low voltage insulation. |
Data Sheet |
Crow Brand |
Tough and rugged coarse weave material. |
Data Sheet |
6F/45 |
Principle features are excellent electrical properties, good dimensional stability and outstanding machinability. |
Data Sheet |
RLF 1 ,2, 3 |
Rolled laminate fabric tube |
Data Sheet |
2F/3/PTFE |
PTFE impregnated cotton weave material, excellent mechanical strength, rigidity, toughness and good machining characteristics with the self-lubricating and low friction properties of PTFE |
Data Sheet |
Paper Laminates |
|
Kite Brand |
First class electrical insulating materials with good dielectric strength and high insulation resistance. Used for a multitude of different applications at low, medium and high voltages, including such items as terminal boards, mounting panels, tag strips, coil formers, insulating sleeves and bushes, busbar supports, tool and instrument handles, coil supports, insulated enclosures, brush holders, insulating spacers and special purpose plugs and sockets |
Data Sheet |
Glass Laminates |
|
10G/24 |
The specially formulated resin of TUFNOL Grade 10G/24 gives exceptional performance in fire tests, over and above the properties found in standard phenolic materials. This results in controlled flammability, good resistance to ignition and excellent low smoke and toxicity values. |
Data Sheet |
10G/40, 41, 42, 44 |
High quality epoxy resin bonded glass fabric laminates offering very high mechanical strength and low moisture absorption, combined with excellent electrical properties, under both dry and humid conditions |
Data Sheet |
10G/50 |
The silicone resin used to bond the laminate gives TUFNOL Grade 10G/50 first class dielectric properties, including high insulation resistance and low loss tangent and permittivity. This ensures good performance in electrical applications at high frequencies. Suitable for use at temperatures up to 200ºC |
No Longer Available |
|
Bear Brand Tufnol Stave sections in dovetail housing
ready for final machining to size. |
|
|
|
|
|
|
|
Underground mine air extractor fan nose sections - Crow Brand |
6F/45 Plates and Washers for use on a railway bogie |
Bear Brand Tufnol Staves in machining jig |
10G-40 Isolating Bushes |
Machining 10G-40 Bushes |
|
The uses for Tufnol grades is only limited by the imagination, we regularly supply the various grades Tufnol for the base plate of 3D printers, wear strips, croquet mallet heads, gears, pipe isolation plates, cryogenic tank supports, fan nose sections, isolation bushes, switch boards, instrument panels, sheave rollers as well as propeller shaft and rudder bearings. |
Tufnol's high resin content components are used in the manufacture of ocean-going vessels for:
- A Bracket bearings
- Stern tubes bearings
- Bow thruster bearings
- Stave bearings
Their resin based materials are unaffected by sea water and have a low swell rate which is very predictable so that they can be very precisely designed and the stress accurately calculated. The bearings are water-lubricated so need no additional lubrication so no oil is used. Tufnol resin based components were originally used for the propeller shaft stave bearings of the QE2.
Tufnol resin materials are accepted by:
- Det Norske Veritas (DNV)
- Lloyd’s Register of Shipping
- The American Bureau of Shipping (ABS)
|
|
Cunard Liner
QE2 |
|
Sterntube Bearing
HMAS Tobruk
Bear Brand Staves |
|
Application Guide for TUFNOL laminates - Typical Choices |
Application Requirement |
Phenolic Paper Grades |
Phenolic Cotton Grades |
Epoxy Cotton and Paper Grades |
Polyester Glass Grades |
Glass Fabric Grades |
General Mechanical |
|
 |
 |
 |
 |
Low Voltage Insulation |
 |
 |
 |
 |
 |
High Voltage Insulation |
 |
|
 |
 |
 |
High Temperature |
|
|
|
 |
 |
Wear Resistance |
|
 |
 |
|
|
Low Water Absorption |
 |
(Bear Brand) |
 |
 |
 |
Dimensional Stability |
|
|
 |
 |
 |
Good Machinability |
 |
 |
 |
|
|
Resistance to the Environment |
|
 |
 |
 |
 |
Low Smoke and Toxicity |
|
|
|
|
 |
|
Designing With Laminates |
TUFNOL laminates are non-metallic engineering materials made from layers of fibrous reinforcement, such as cotton cloth, paper or woven glass cloth, which are bonded together with high quality thermosetting resins. In manufacture, the paper or fabric is first impregnated with the resin. Then, layers of this impregnated material are pressed together under high pressure and heated to about 160oC. This causes chemical changes in the resin, making it harden, and fusing the laminate into a tough, strong solid. By using alternative resins with different types of reinforcements and additives, a range of grades is created, with types to suit a wide variety of applications.
Also, by rolling or shaping the impregnated layers before pressing, stock shapes such as rods and tubes can be moulded. The resulting TUFNOL laminates combine mechanical strength with excellent chemical and weather resistance. They are rigid, with high strength and low weight and some grades can be used in temperatures ranging from around absolute zero to over 250ºC. They are also extremely useful for electrical and thermal insulation. |
Designing Components |
Choice of Laminar Direction |
|
|
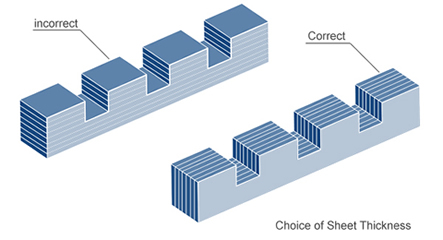 |
The designer who is considering using a laminate for a particular application should always bear in mind the fact that the material has a laminar structure and therefore has different strengths in different directions relative to the layers. It is therefore essential to ensure that the correct section of material is chosen, so that the laminations lie in the best direction to deal with the stresses involved. Even where components are not required to withstand any load in use, machining to produce the component itself causes stress. Lack of consideration for the structure of the laminate can lead to fracture during production, handling or transit. Figure 2 illustrates several examples where the laminar construction has influenced the choice of section away from the most immediately obvious. Many laminates are slightly sensitive to stress concentration and, as with other materials, wherever possible it is good design practice to avoid stress-raising features, such as sharp internal corners or sudden changes in section. |
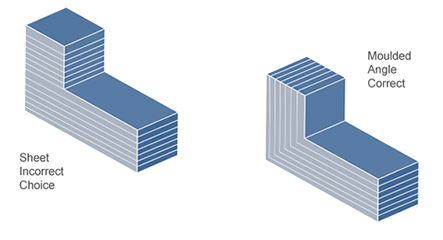 |
|
Tolerances on standard sections |
|
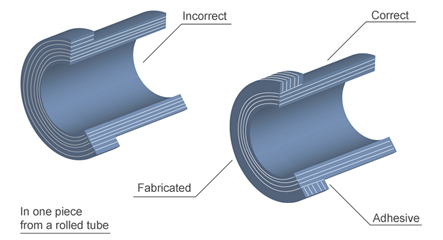 |
High-pressure laminates cannot be moulded to precisely accurate dimensions and, when selecting sizes of standard materials for ordering purposes, an allowance should be made for the possible variations in, for example, the moulded thickness of a sheet or the concentricity of a rolled tube. These are usually greater with the coarser reinforcing materials and reference should be made to the British Standard relevant to the particular type of laminate. |
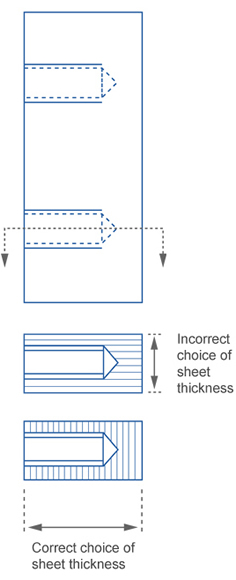 |
|
Machining Tolerances and Finishes |
|
Owing to the nature of the material, components cannot normally be machined to the finest tolerances achievable with metals; however, the surface of a laminated plastics component has a slight resilience, which usually renders very fine tolerances unnecessary for good fits to be achieved. Laminated bushes require a greater interference than metal bushes so that the same machining tolerance becomes much less significant. On the other hand, when inserted, the laminated bush may compress slightly on the bore, so an allowance may have to be made for this when determining the size to be machined. Similarly, the fibrous nature of the reinforcement causes considerable difficulty in achieving fine surface finish readings on machined faces. This obviously varies with different grades but, for example, a first-class milled face on a medium weave fabric laminate may record a surface finish of 3 to 4 micrometers (125 to 160 micro inches) and even prolonged polishing may only reduce these figures by half. Once again, the resilient surface of the laminate usually makes fine finishes unnecessary. The milled face mentioned above would be entirely suitable as a bearing surface, without polishing |
The information above is extracted from Tufnol literature |
|
Also available from C.E.& A. Co |
|
 |
Also available from C.E.& A. Co. |
- - Propeller Shaft and Rudder Bearings - -
- - Propeller Shafts and Sterntubes - -
- - Rudder Carrier Bearings and Rudder Trunks - -
- - Water or Oil Lubricated Shaft Seals - -
- - Deck Machinery - -
- - Chockfast Orange - -
- - Spurs - Rope, Net and Weed Cutter - -
- - PolyFlex Engine Mounts and Couplings - -
- - Vickers Marine Oils - -
- - Arctic Steel - Stainless Steel Water Strainers - - |
|
Home Page |
For further information, or to purchase Tufnol please contact us. |
|
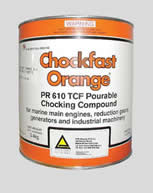 |
Chockfast Orange
Epoxy Chocking Compound |
|
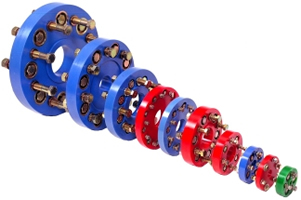 |
Polyflex Engine Mounts
and Couplings |
|
|
 |
5 Schenker Drive, Royal Park.
South Australia. 5014 |
Ph: 08 8240 0777 |
Int. Ph: +618 8240 0777 |
E-mail: ceaco@ceaco.com.au |
|
|
|
|
|
|